Skip to forum content
The NASTE Forum
Welcome to the forum of the Northwest Slot Track Enthusiasts!
You are not logged in. Please login or register.
Active topics Unanswered topics
Search options (Page 124 of 230)
Topics by wb0s User defined search
Posts found: 3,076 to 3,100 of 5,742
by wb0s » Sun Jun 08, 2014 7:36 pm
The front axle mount attaches to the center section uprights with two allen head cap screws. The axle mount holes are threaded. The slotted holes in the center section uprights allow for vertical adjustment of the front axle. Ride height and ground clearance can be adjusted to different tire sizes if desired.
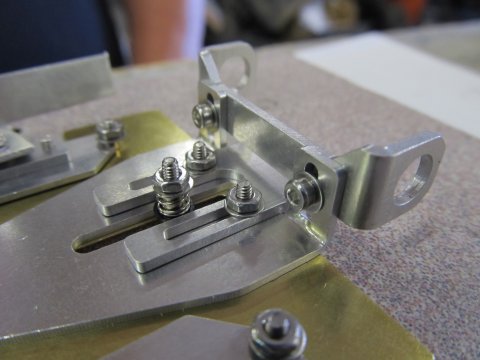
The front axle mount holes are also metric and like the rear axle mount holes, must also be reamed out to accept the bushings to fit standard 1/8 or 3/32 inch axle bearings.
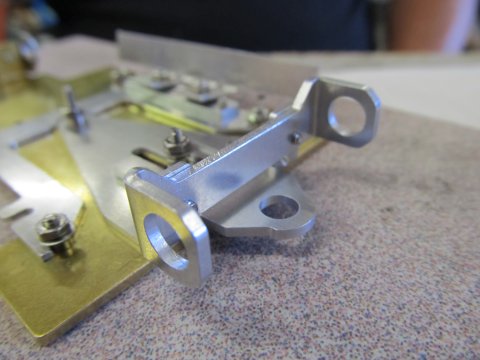
This is the completed center section, guide flag tongue, and front axel mount.
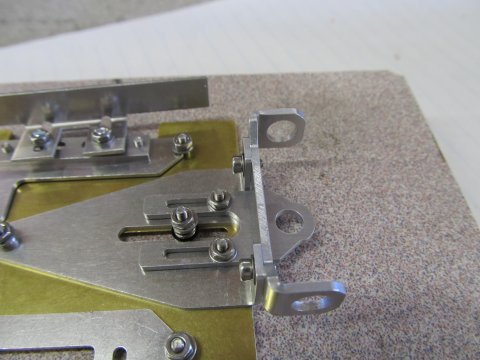
by wb0s » Sun Jun 08, 2014 7:21 pm
Insert a tall flat head screw through the middel rear slotted hole in the brass chassis. This screw will be counter sunk and flush with the bottom of the chassis, and will secure the rear portion of the center section. Install a steel spacer over the screw. The spacer's O.D. is slightly smaller than the I.D. of the hole in the center section's rear mounting position. Install a spring over the screw and spacer. The bottom of the spring rests on the top of the center section. Install a washer on top of the spring, the spring will be captured between the center section and the washer on top. Install a nut on the screw to complete the assembly.
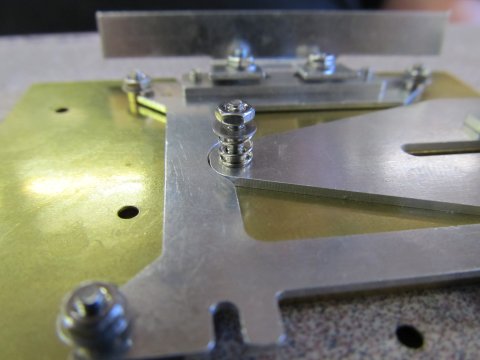
Like the front of the center section's mounting assembly, this rear mount can also be adjusted for movement and spring tension by tightening or loosening the screw and nut.
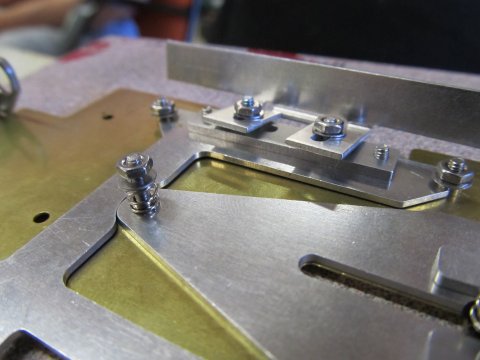
by wb0s » Sun Jun 08, 2014 7:07 pm
A long flat head screw is installed through the brass chassis in the middle slotted front hole. The flat head screw is counter sunk into the bottom of the brass chassis. The slotted holes in the brass chassis allow for wheelbase adjustments to accommodate different bodies.
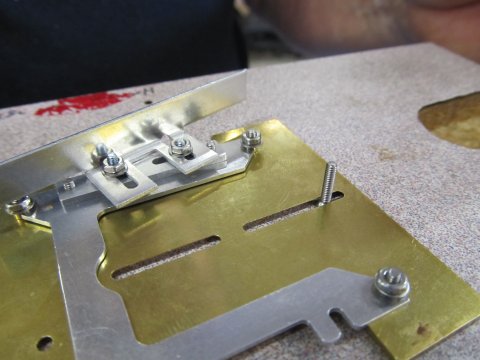
The center section with the guide flag tongue mounted is installed over the screw.

A long steel spacer is installed over the screw. The spacer's O.D. is slightly smaller than the I.D. of the slotted hole in the center of the center section. The spacer keeps the center section centered on the brass chassis. A washer is installed over the spacer and screw, and rests on the center section. The washer's I.D. is slightly larger than the O.D. of the spacer. One of the springs is installed over the spacer and screw. The bottom of the spring rests on the washer positioned on the top of the center section. A washer with an I.D. the size of the screw is placed on top of the spring.
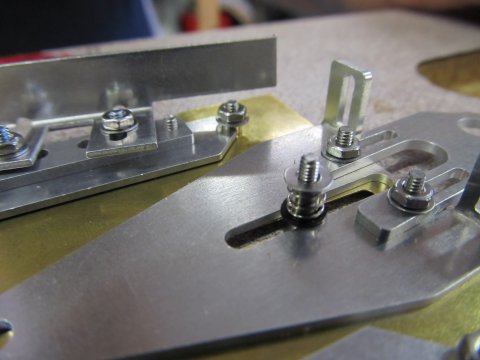
A nut is installed on the screw above the washer. This assembly secures the front axle mount and guide flag tongue to the brass chassis, while providing adjustment for travel and spring rate by tightening or loosening the screw and nut assembly.
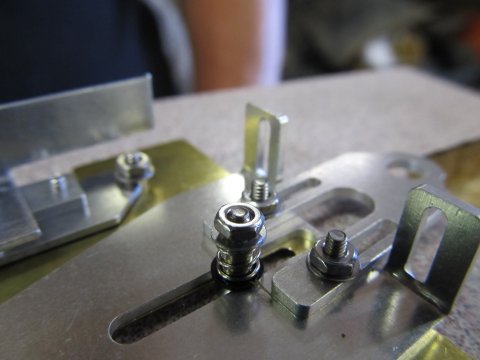
by wb0s » Sun Jun 08, 2014 6:50 pm
This is the center section of the chassis which is spring mounted. This center section will have the guide flag tongue and front axle mount secured to it.
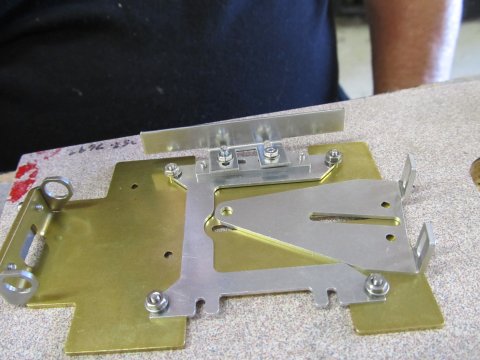
Three springs came with this Scholer chassis kit. There were two standard springs and one heavier spring. We used the two standard springs for this initial assembly. Testing of the finished car would determine which springs work best in a particular application.
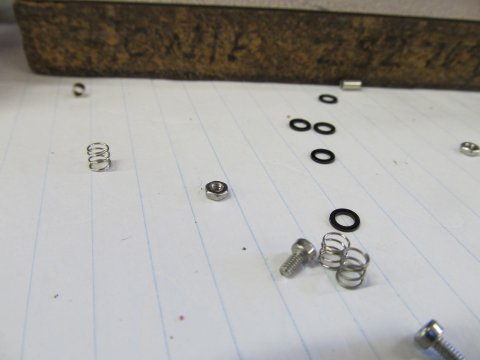
The guide flag tongue is secured to the center section using flat head screws, washers, and nuts. The flat head screws are counter sunk on the bottom side of the center section.
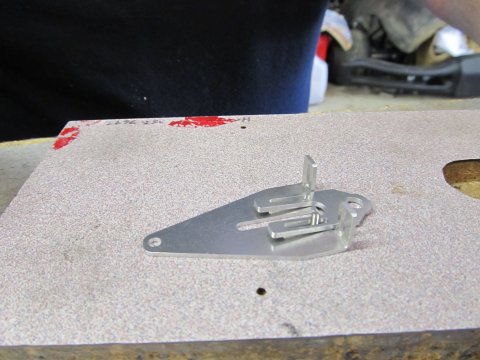
The screws used to mount the guide flag tongue must be tight. There is a lot of force on the guide flag mount, so the screws and nuts must be kept tight. There is room to add two additional screws , washers, and nuts to provide additional strength if desired. Blue Locktite would again be an option.
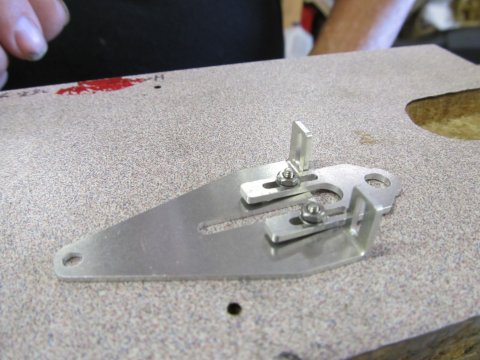
by wb0s » Sun Jun 08, 2014 6:32 pm
This is the rear axle mount. The holes for the axle bearings are metric and must be reamed out to accept a bushing to use standard sized bearings for 1/8 or 3/32 axles. The holes can be reamed or enlarged using a round file. Go easy it doesn't take much.
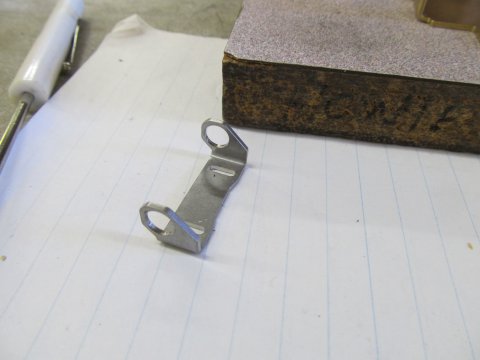
These are the bushings used to convert from metric bearings to standard for 1/8 and 3/32 inch axles. These are made by Slick 7, and the part number is: S7-142. They are sold in pairs.
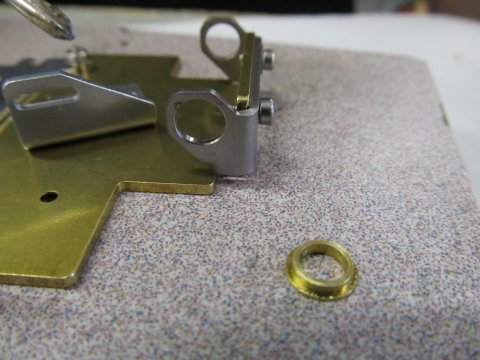
There are two theaded holes in the rear vertical portion of the brass chassis where the rear axle mount is positioned (left side of the chassis in this photo). Please note that the H rattle pan is installed correctly in this photo!
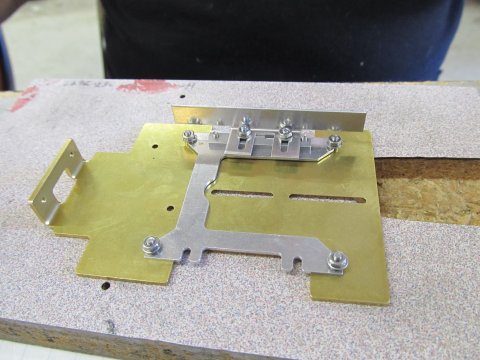
The rear axle mount is secured to the brass chassis with two allen head cap screws. The mounting holes in the mount are slotted to allow vertical adjustment, which raises the axle up and down to adjust ride height and ground clearance at the bottom of the chassis.
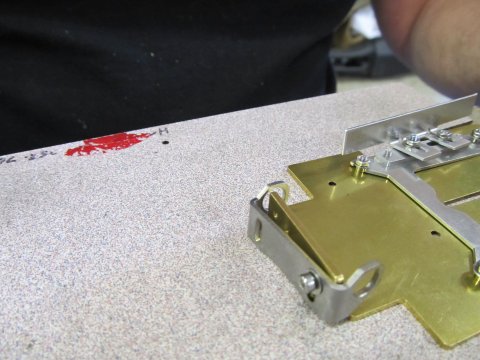
The rear axle mount screws must be tight to keep the axle mount from moving out of position. Again, the application of Blue Locktite is an option.
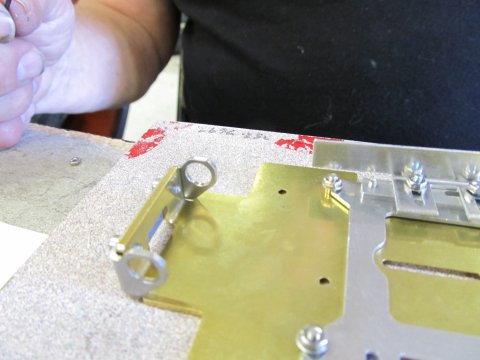
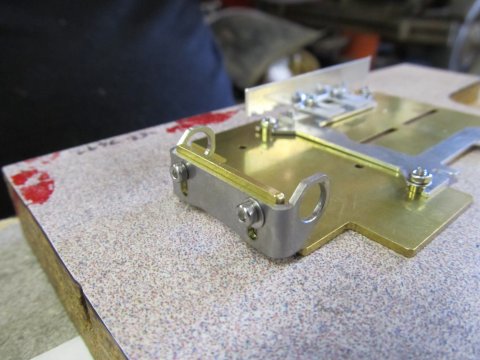
by wb0s » Sun Jun 08, 2014 3:32 pm
These phillips round head screws are used to mount the body mounts to the rattle pans.
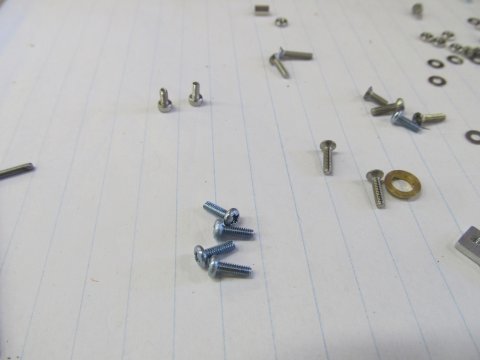
If you are installing side pans instead of the threaded plates, and depending upon how you intend to mount the body, you may or may not choose to use these body mounts.
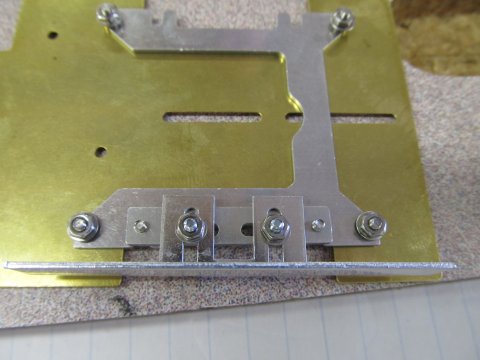
The phillips round head screws, nuts and washers secure the side body mounts to the threaded plate.
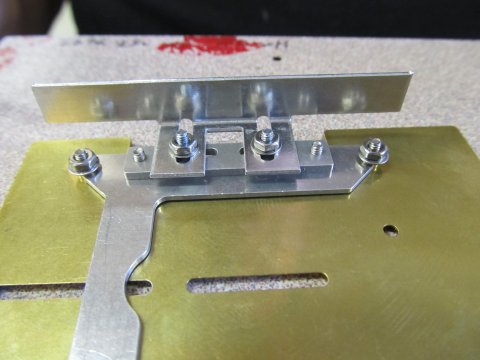
The slotted holes in the threaded plate and the body mounts allow for adjustments front to rear, and side to side to fit most any model car type body.
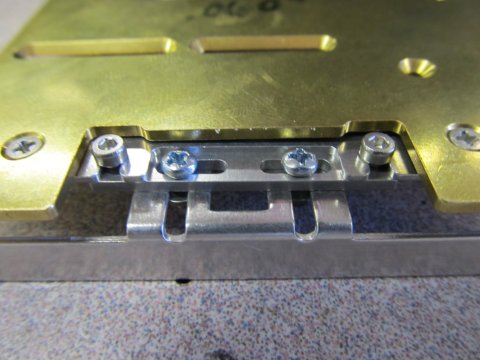
y wb0s » Sun Jun 08, 2014 3:23 pm
Here's another close up shot of a brass side pan installation on another Scholer chassis. You can also see the steel wire bracing of the H rattle pan.
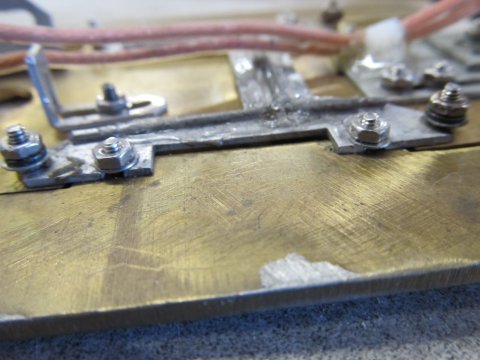
This is the bottom side of the chassis. You can see how the screws attaching the brass side pans to the H rattle pan are counter sunk into the bottom side of the brass side pan.
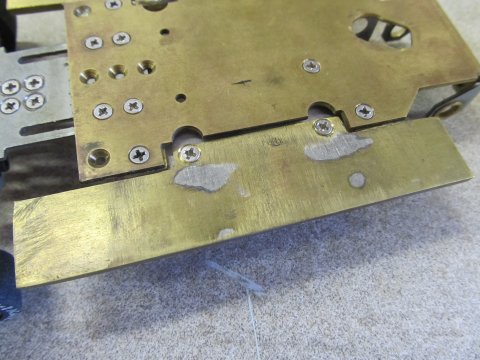
Side pans must be cut, ground and filed to fit the chassis. The side pans should have free movement when attached to the H rattle pan. Any interferrence between the pans and the chassis can cause the pans to bind and catch which can have negative effects on handing characteristics. We generally make side pans out of .062 or .090 inch strip brass. Some racers have also had good results using aluminum side pans.
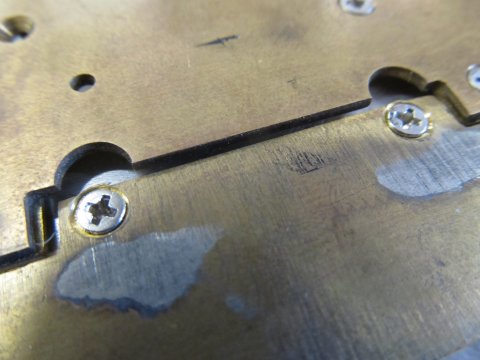
by wb0s » Sun Jun 08, 2014 3:12 pm
This is the threaded plate. The two outboard holes are threaded for the screws that secure it in place on the H rattle pan. If you are building side pans for your chassis the side pans will be installed in leui of these pieces.
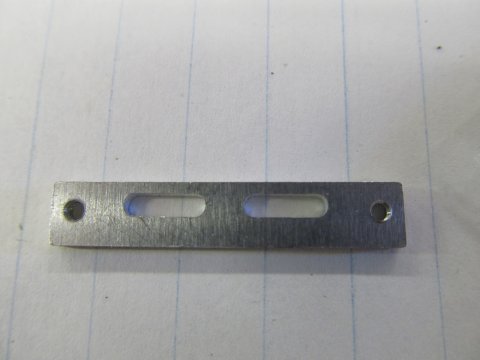
The threaded plates are installed using the allen head cap screws.
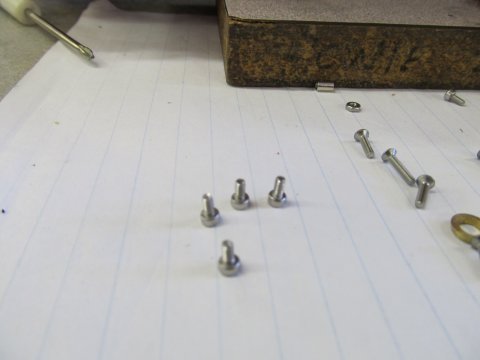
The cap screws fit into place in the notches on the outside edges of the H rattle plate.
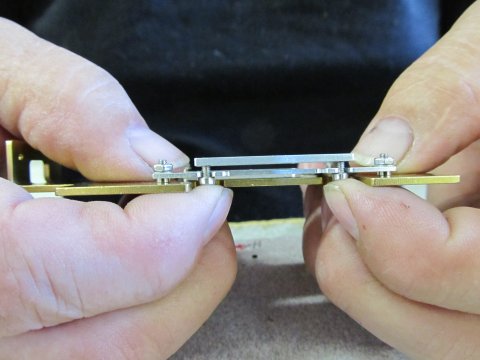
This photo shows the threaded plate in postion on the H rattle pan. YES, the H rattle pan is still on the brass chassis backwards. The screws must be tightened to hold the threaded plate to the H rattle pan securely. Again the use of Blue Locktite is an option.
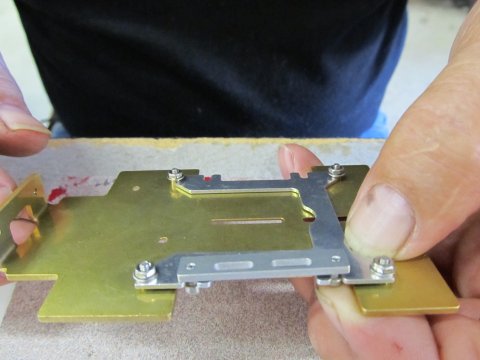
This photo shows a chassis with brass side pans installed. The brass side pans are secured directly to the H rattle pan using flat head screws and nuts. The flat head screws are counter sunk into the bottom side of the brass pans. To install brass pans additional screws and nuts must be purchased from a hardware store.
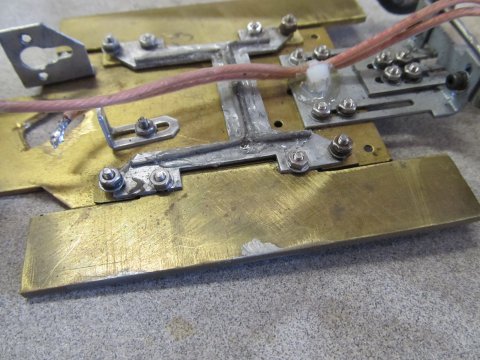
by wb0s » Sun Jun 08, 2014 3:00 pm
After the flat washer is in place, install a nut over the screw to secure the spacer assembly to the brass chassis.
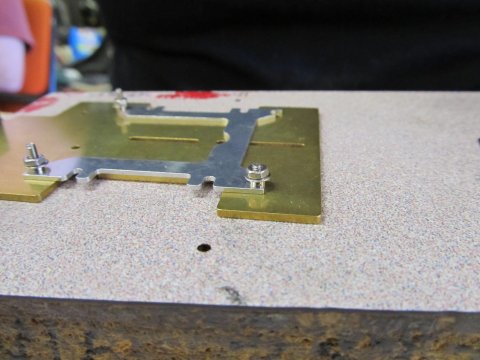
Be sure to use the screws that are long enough to capture the spacer, washer, and nut after the screw is inserted through the brass chassis.
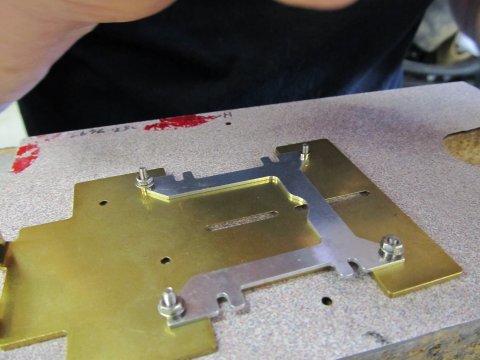

After all four spacer assemblied are secured in place the H rattle pan will be captured and held in place on the top of the brass chassis. The H pan should move freely up and down or verically above the brass chassis. The brass chassis stops the downward movement of the H rattle pan, and the flat washers stop the upward movement of the H rattle pan. Be sure all the srews and nuts are tight!
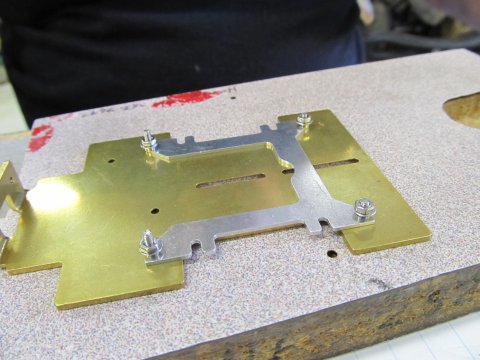
by wb0s » Sun Jun 08, 2014 2:50 pm
This is how the H rattle pan fits up against the spacers and screw assembly. Again in this photo the H rattle pan is positioned backwards.
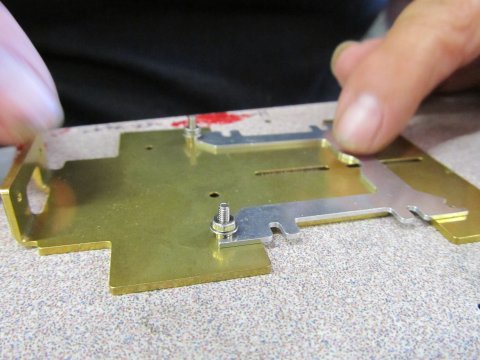
With the H rattle pan in position against the rear two spacers (yes this one is still pictured backwards), install the two screws in the front two holes in the brass chassis.
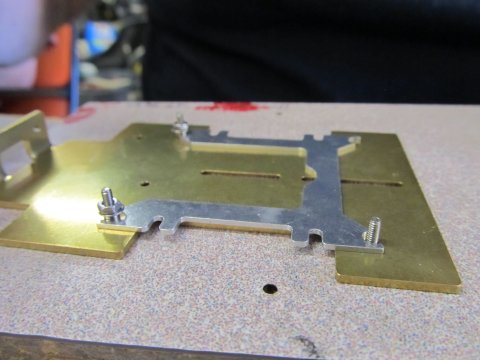
Just like the rear two spacer assemblies, install a short spacer over each screw for the front spacer assemblies.
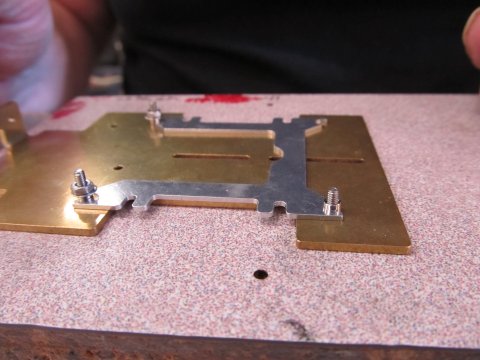
Install a flat washer over the screw onto the top of the spacer just like each of the rear spacer assemblies.
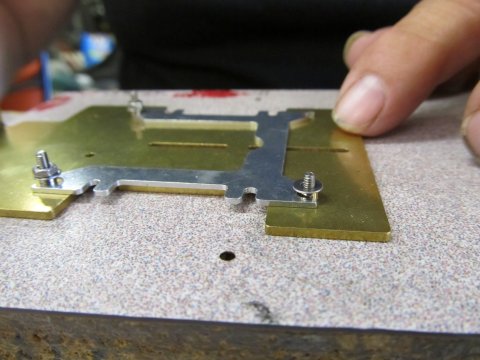
by wb0s » Sun Jun 08, 2014 2:41 pm
The short metal spaces are placed over the screws to sit on the brass chassis. These spacers are what allow the rattle pan or H piece to have some vertical movement after the piece has been secured in place. You will use 4 of these spacers for mounting the H rattle pan. The first step in mounting the H rattle pan is installing two of the four mounting screws and spacers.
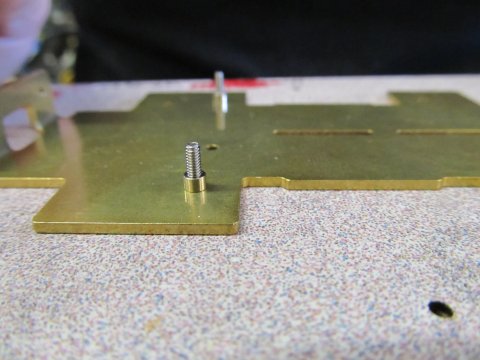
After the screws and spacers are in place, install a flat washer over the screw. The flat washers will sit on top of the spacers on each of the four screws. Again, only install the two rear screws or the two front screws at this point in the assembly proceedure.
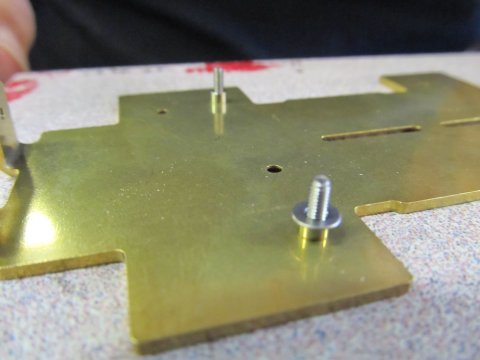
After the flat washers are in place install a nut onto the crew and tighten it down over the flat washer and spacer.
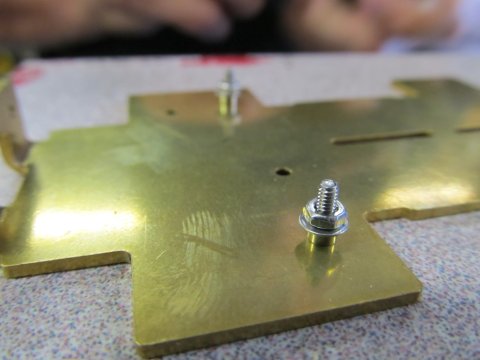
Use a screw driver and wrench or pliers to be sure the pieces are tight. A small amount of Blue Locktite is an option that can be used on the screw threads to ensure the parts will not come loose.
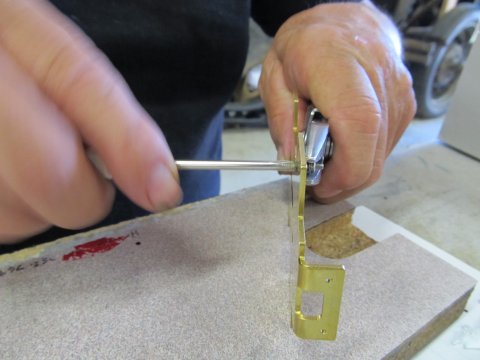
by wb0s » Sun Jun 08, 2014 2:30 pm
This is the Scholer H-Trager positioned on top of the Grundplatte. Anyway that's what they're listed as on the Scholer directions which are written in German. We like to call them the brass chassis and the rattle pan. In this photo the aluminum rattle pan is positioned on top of the brass chassis. Please take note that in this photo the rattle pan is backwards from proper installation.
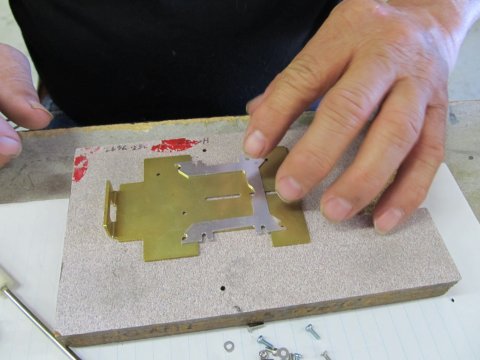
Howie suggests reinforcing the aluminum rattle pan as the H shaped pice is easily bent. Use epoxy or JB Weld to glue pieces of steel wire onto the top of the H piece as shown in the photo. The wire can be glued in any configuration you think will add support to the rattle pan, .055 or .062 inch diameter steel wire is sufficient.
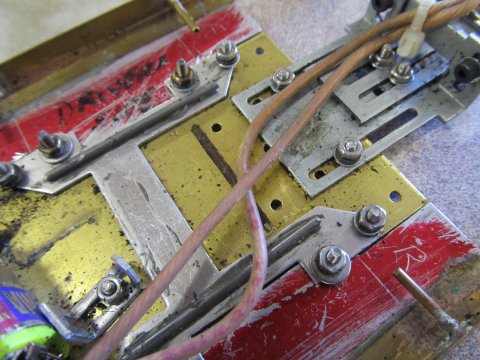
The longer flat head screws are used to mount the rattle pan. The screws are inserted through the brass chassis. The heads sit flush with the bottom of the chassis as the holes are counter sunk.
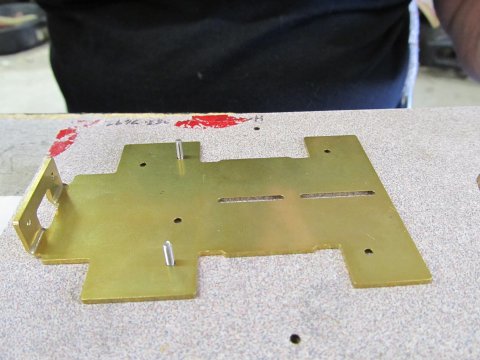
by wb0s » Sun Jun 08, 2014 10:27 am
This is the assembly proceedure for the Scholer Intruder chassis. There are other types of Scholer chassis, but the pieces for each and the assembly proceedures are similar.
Here are the parts contained in the package.
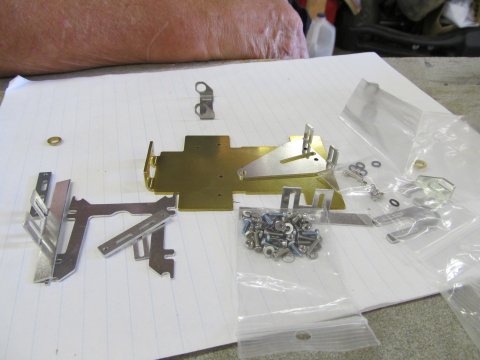
The screws have different head types, as well as different lengths.

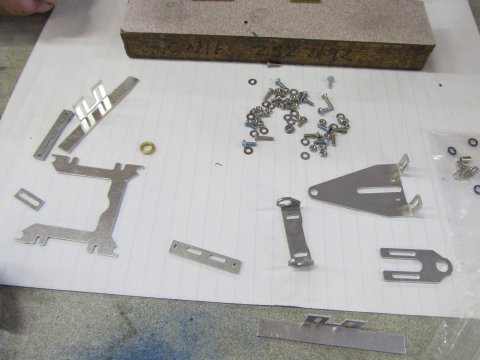
Here's a parts list Howie put together to help us get started on building a hardbody chassis:
Brass - available at some hardware stores:
.090 inch x 3/4 inch wide brass strip - used for side pans = 1 @ 12 inch length
.090 inch x 1 inch wide brass strip - used for center section = 1 @ 12 inch length
.040 inch x 1/2 inch wide brass strip - used for guide flag tongue = 1 @ 12 inch length (can substitue manufactured steel guide flag tongue if desired. Available at most slot car shops or online)
.062 inch x 1/4 inch wide brass strip - used for front axle mount = 1 @ 12 inch length
1/8 inch or 3/32 inch I.D. round or square tubing - used for front axle mount = 1 @ 12 inch length (if using axle bearings use 3/16 inch tubing for 3/32 axel, or 1/4 inch tubing for 1/8 inch axle).
3/32 inch square tubing - used for chassis hinges = 1 @ 12 inch length
1/16 inch square tubing - used for hinges and stops = 1 @ 12 inch length
.055 inch steel wire - used for hinges and mount points = 1 @ 12 inch length
.062 inch steel wire - used for hinges, mount points, and stops = 2 @ 12 inch length
3/32 inch angle brass strip - used for body mounts = 1 @ 12 inch length (can substitute 1/8 inch angle)
Specific Slot Car Parts:
1 motor/axle mount for the specific motor you plan to use, and for the motor configuration you plan for your chassis (i.e inline, anglewinder, side winder. Refer to the rules for the class you are building for).
2 axles 1/8 inch or 3/32 inch (refer to class rules).
1 guide flag.
1 guide flag mount (or substitute scratchbuilt).
2 pickup braids (installed in guide flag).
4 bearings or oilites (one pair for each axle - 2 front & 2 -rear. Can eliminate if using axle I.D. tubing).
1 motor (refer to rules).
2 motor lead wires (approx. 12 inches total = 6 inches each).
1 crown gear (for inline motor) or spur gear (for anglewinder or sidewinder).
The previous posts to this topic were copied over from the Northwest True Scale Racers site with Howie's permission. The NTSR site is scheduled to close down at the end of this year. I will be copying over as much of the great information posted there as possible in the next few months. =====Bill
by howie » Thu Dec 15, 2016 12:52 pm
Working on an Xfinity NASCAR for Blake. Beings we voted to go to a Lexan Gen 6 NASCAR bodied car, the only one's we could find are form Pattos, the bodies are rough, the wings are worse, but that is what we have to work with. So I decided to make the wing out of .005" sheet styrene by Evergreen. I cut it and bent it according to the pictures of the 1 to 1 NASCAR and using a strong double stick tape by Scotch, stuck it to the back of the car. When I am done with the car I will post a picture, it is a Dodge Challenger.
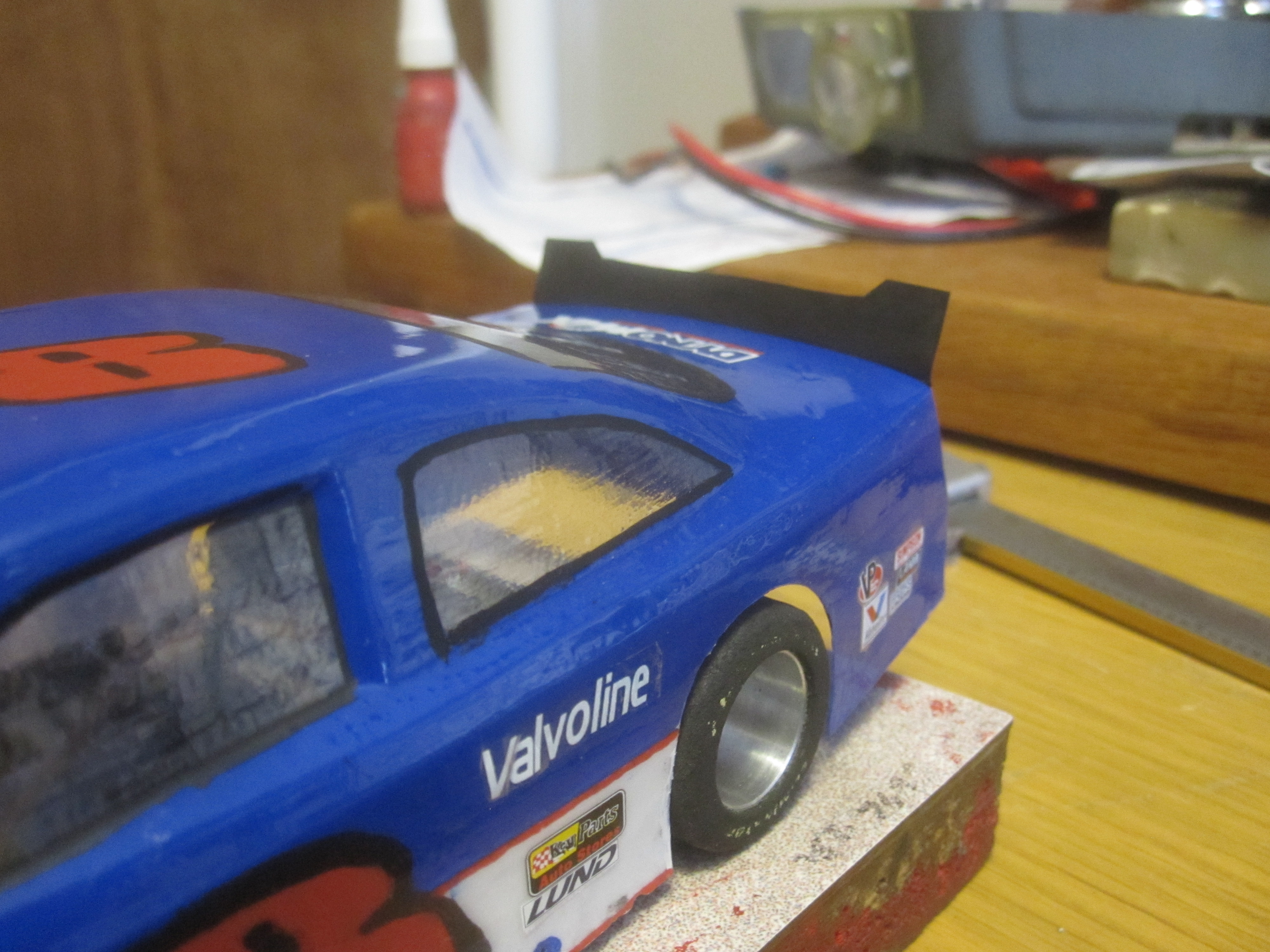
by racerbob9 » Sat Nov 05, 2016 12:37 pm
Finally got a GT3 body done! Looking forward to a new season.
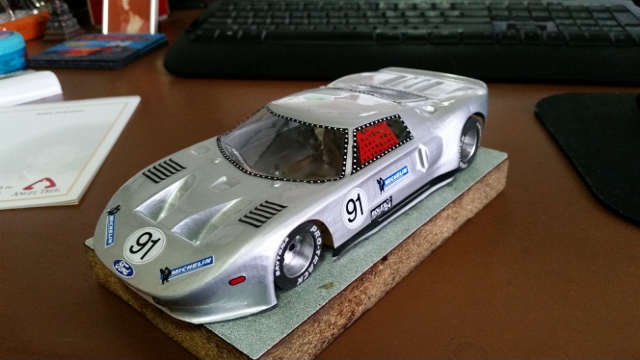
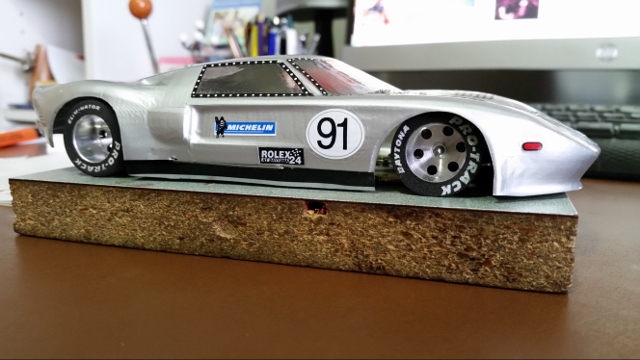
by howie » Sun Oct 02, 2016 7:21 pm
Finally finished this car, it was going to Dayle but it will be Blake's new Xfinity NASCAR. The paint scheme is simple as this body will be raced one time only in the Rapid 500. After that race the NASCAR"s will be going to Lexan bodies for the 2017 season and beyond.
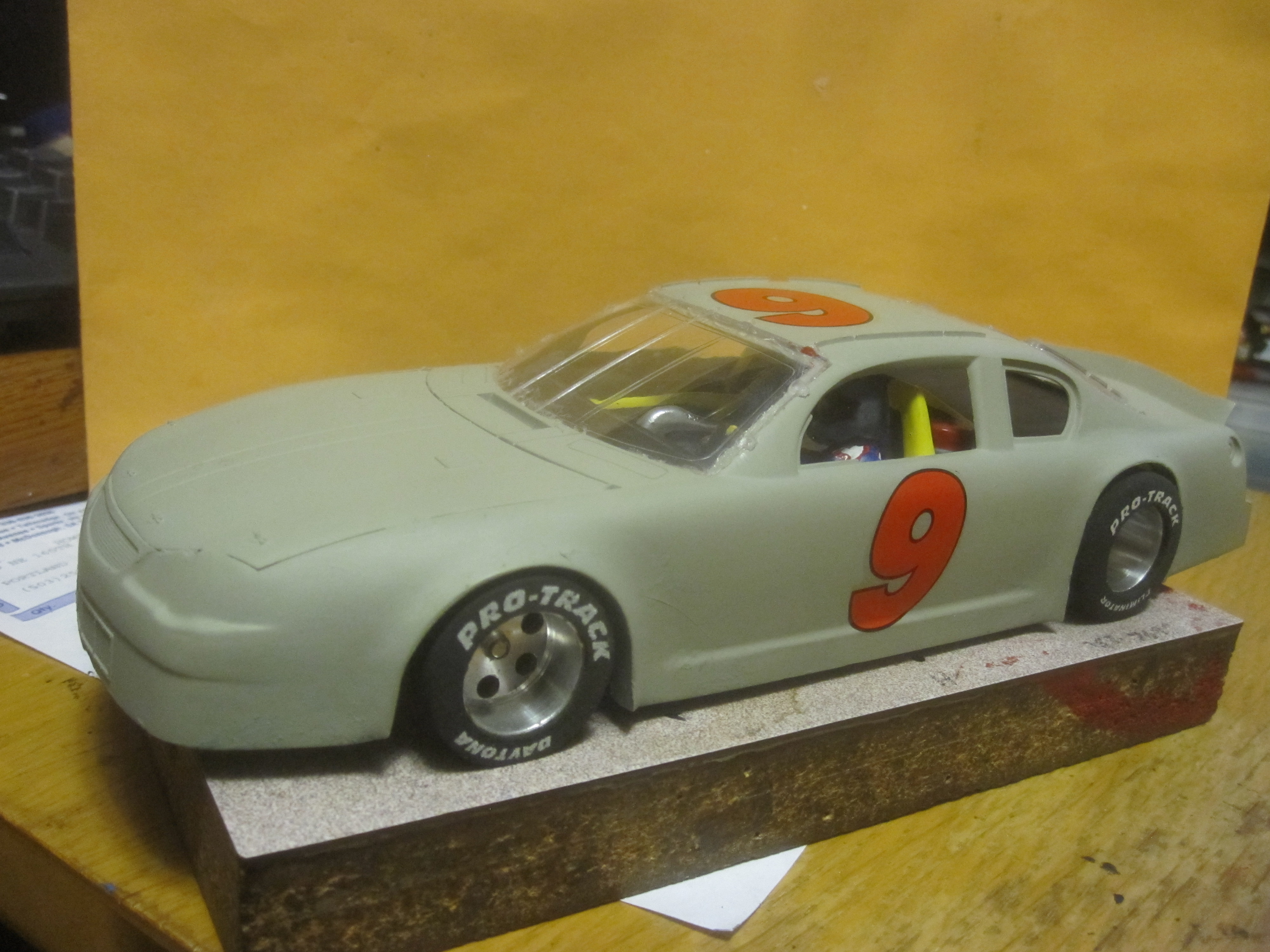
by howie » Fri Apr 22, 2016 3:29 pm
In the process of getting Blake a TA2 chassis ready for tomorrow's race. This chassis is a Slotting Plus # SP800001. I used 1/4" brass angle and soldered it to the chassis side mounts. I cut the width of the side mounts to accommodate the body. For the race tomorrow Blake will be taping the body on, but I will make body mounts to do away with the tape method. The race tomorrow for the TA2 is a fun race and so his car will not be completed, but will be racing. This chassis is also going to be used for his NASCAR, the only thing he will have to do is change motors and bring the pans a little farther out, easy to do as they are mounted in a slot to slide in and out! Tracking and wheelbase are the same.
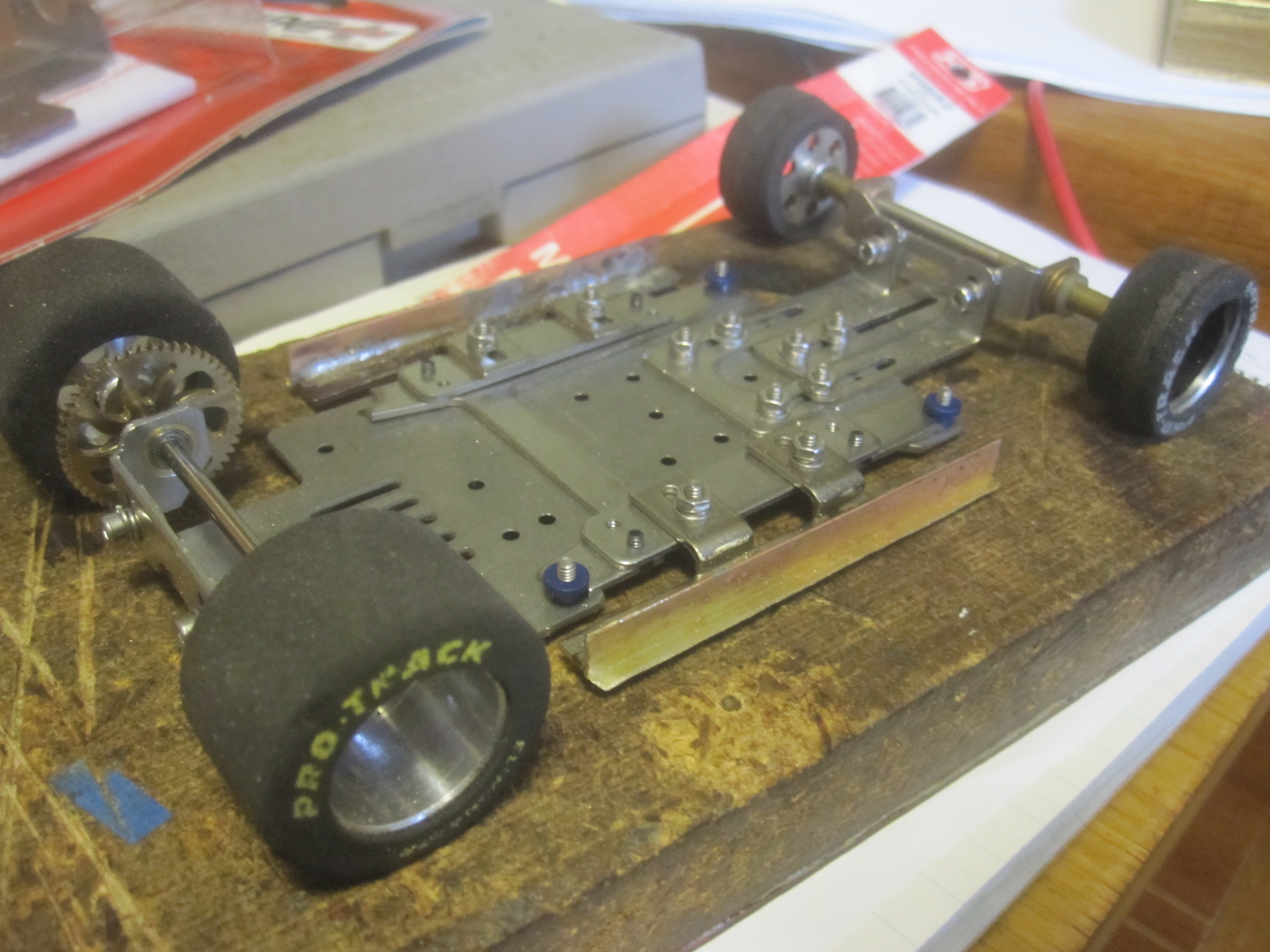
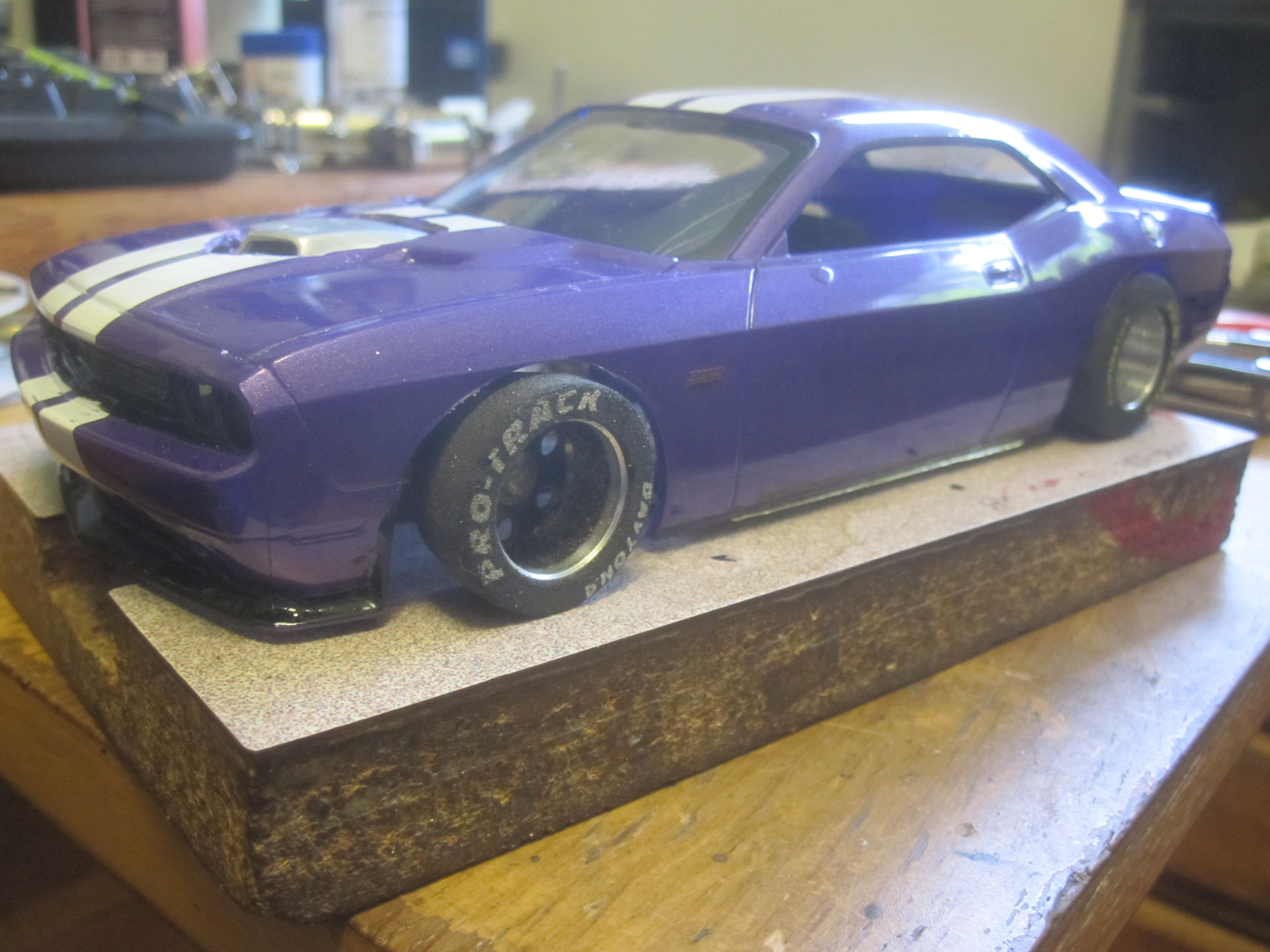
by wb0s » Thu Apr 14, 2016 10:25 am
That body really looks good on there Howie!
by howie » Thu Apr 14, 2016 9:21 am
Currently working on a new Can-Am car. Don't know what brand this chassis is out of my old chassis drawer but it will be used on this new Lexan body from Blue Groove: Google it. They do a lot of bodies for R/C cars also. This body is a .030" Lexan Chaparral. It is almost like working with a hard body! These bodies should last a long time. In case you want to spray paint, the blue coating prevents over spray on the outside of the body. The blue coating easily peals off. The body is rather narrow for this chassis: 2.970" at the bottom. The chassis is 3.190". So if my math is right I will have to narrow the chassis by .220". The body is really nice and detailed, I see no flaws in it. I already roughed out the wheel wells. Once again I will fabricate an adjustable rear axle mount.
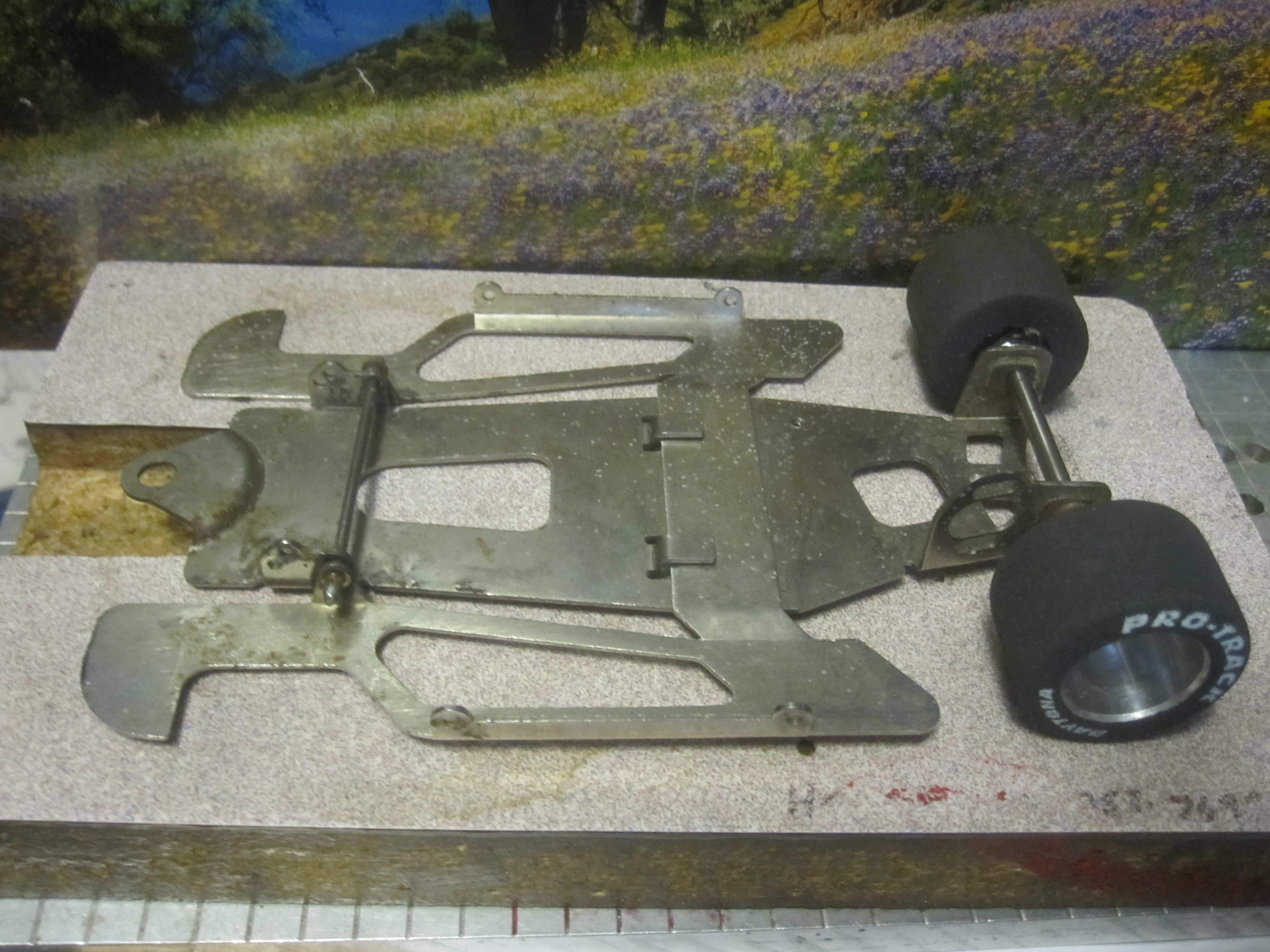
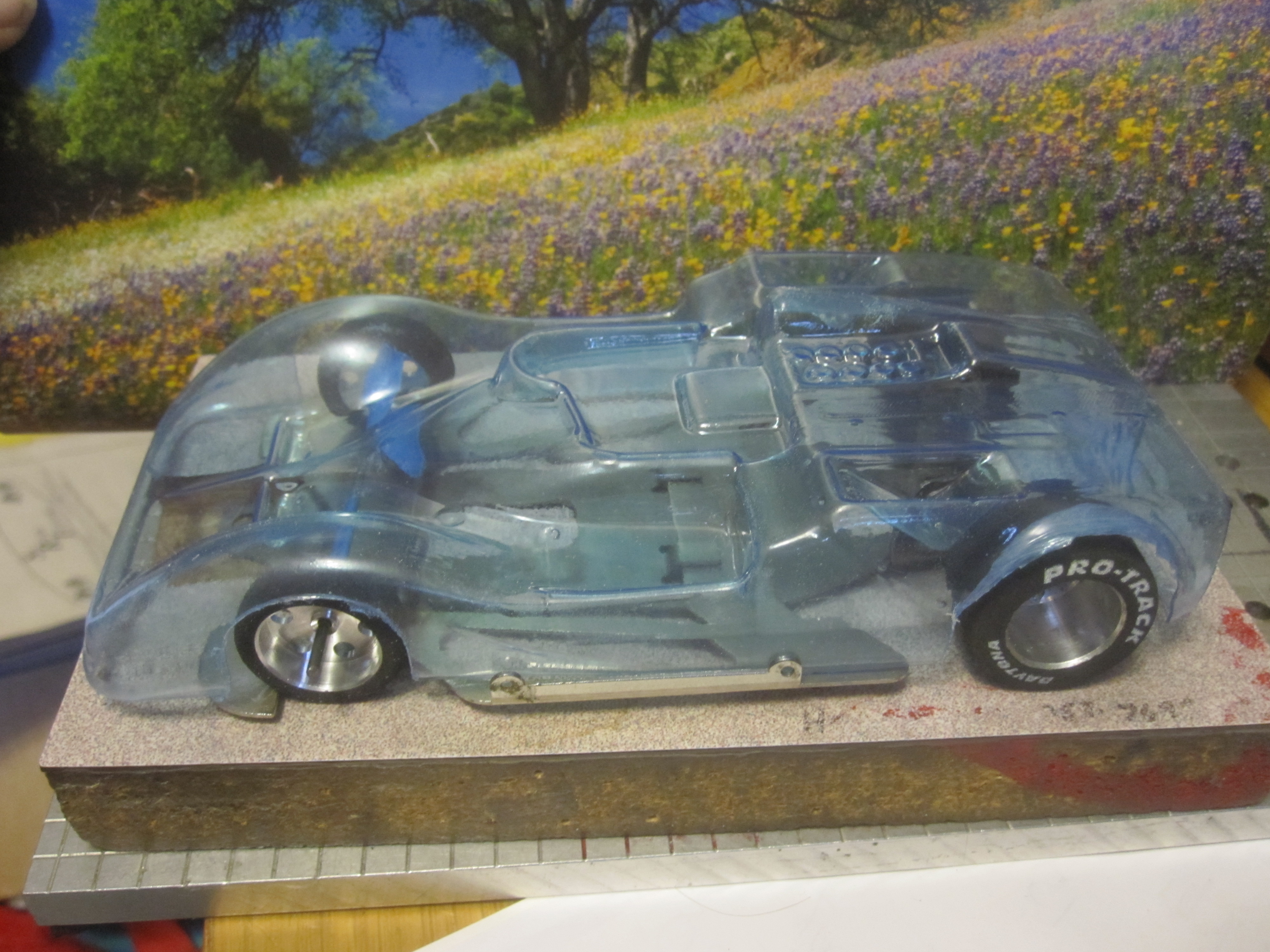
by howie » Thu Apr 14, 2016 9:12 am
Very unique body mounting Bill, gets away from the not so cool taping method and that is a good thing! I have never liked the taping method, but it is easy and I suppose that is why it is done so much!
by wb0s » Mon Mar 21, 2016 6:02 pm
I've also been working on my Modified. Howie built me a chassis, which I appreciate greatly, and I am currently working on the body and detail pieces. Here is the body mounting system I used. Using JB Weld I attached traction magnets from 1/32 scale slot cars to the chassis. I Attached small L shaped pieces of sheet metal to the inside of the body, also secured with JB Weld. This system seems to hold well enough I think I'll try it on my Sportsman car also.
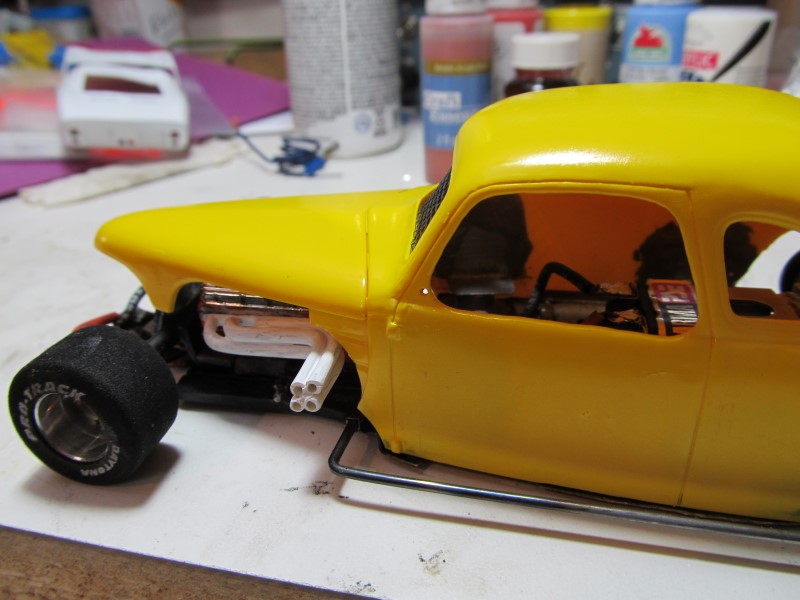
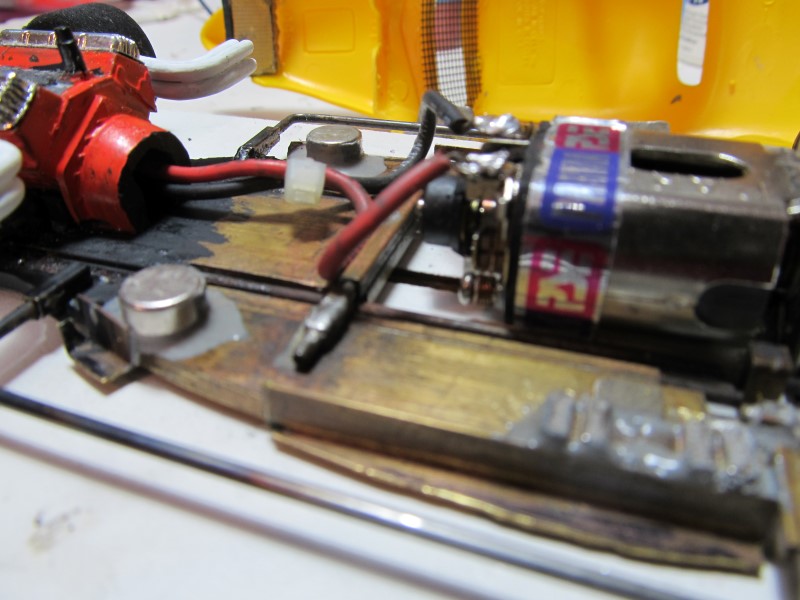
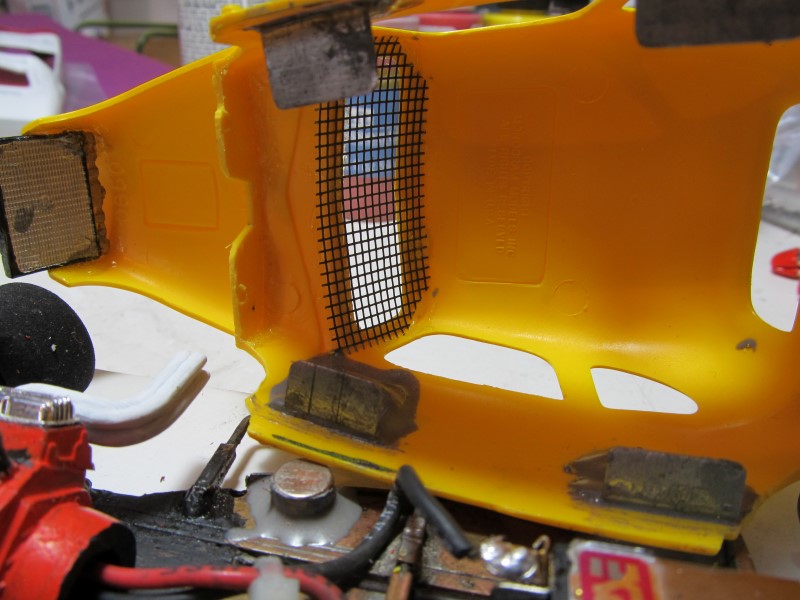
by wb0s » Mon Mar 21, 2016 5:57 pm
I have LOTS of projects on the bench! Here's my TA2 Camaro waiting to be finished. I'm in the process of adding extra width without making fender flares.
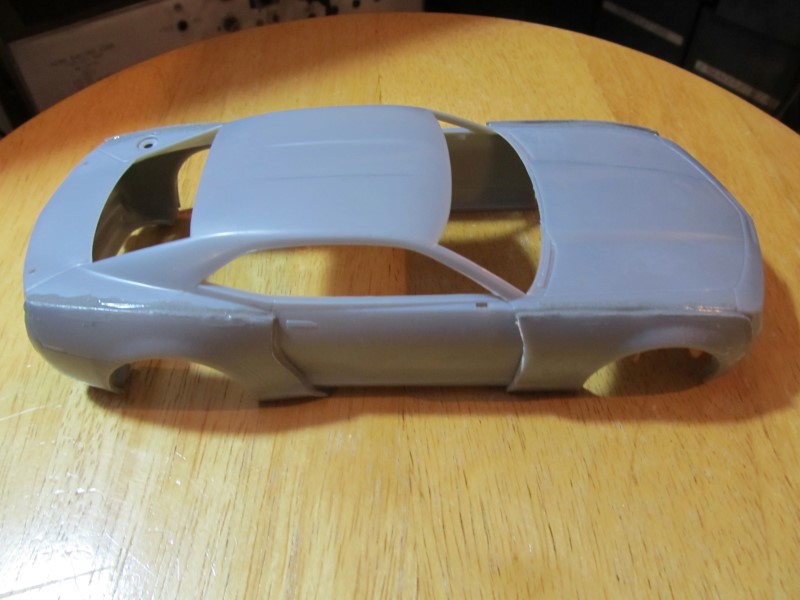
by howie » Sat Mar 19, 2016 9:33 am
Making progress on the second F1. A simple "L" bracket out of .032" brass with two holes drilled in it and soldered to the chassis. As you can see this chassis will have adjustable ride height in the rear. I am using the Sloting Plus axle bracket part # SP902633. Next step is an axle set up for each front wheel.
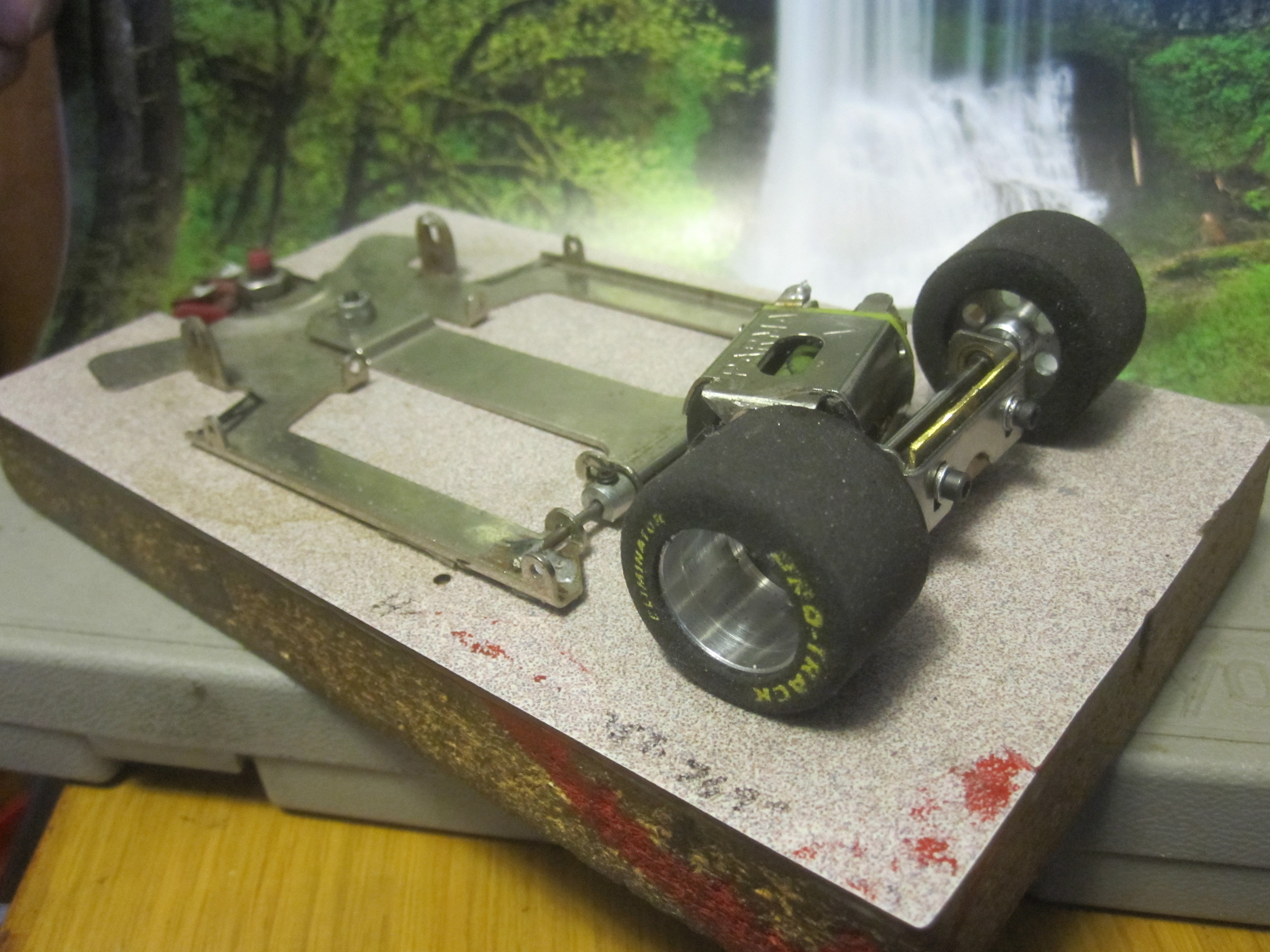
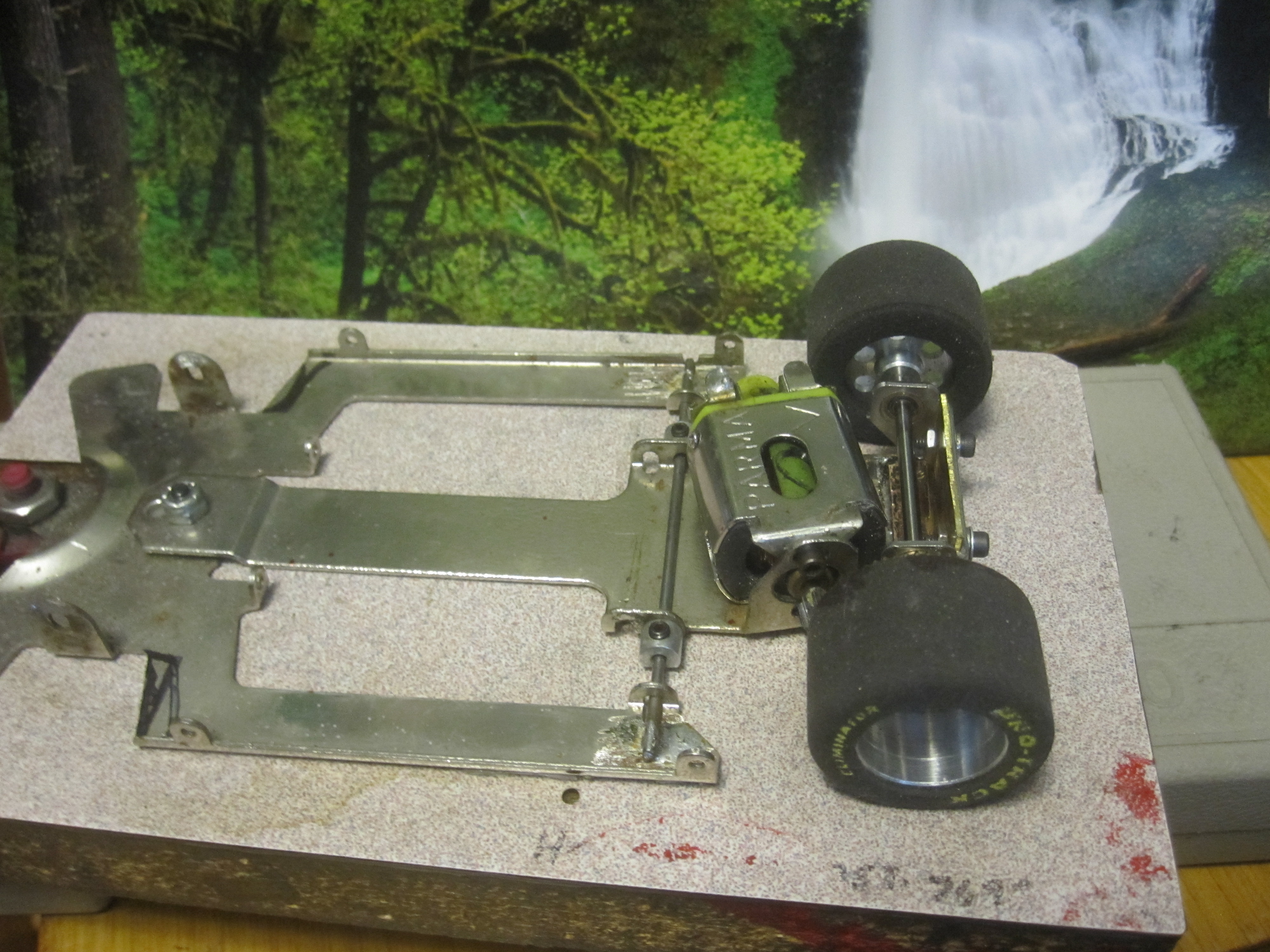
Posts found: 3,076 to 3,100 of 5,742